Optimierte Produktentwicklung
Ob ein entwickeltes Produkt den geforderten Qualitätsansprüchen entspricht, kann oft erst durch experimentelle Tests überprüft werden. Dafür werden erste Prototypen des Produktes hergestellt, welche anschließend geprüft und optimiert werden. In der Regel erfordert ein Produkt mehrere Prototypeniterationen, bis das Produkt die Marktreife erzielt. Dieser Prozess ist auf Grund des hohen Aufwandes sehr kosten- und ressourcenintensiv.
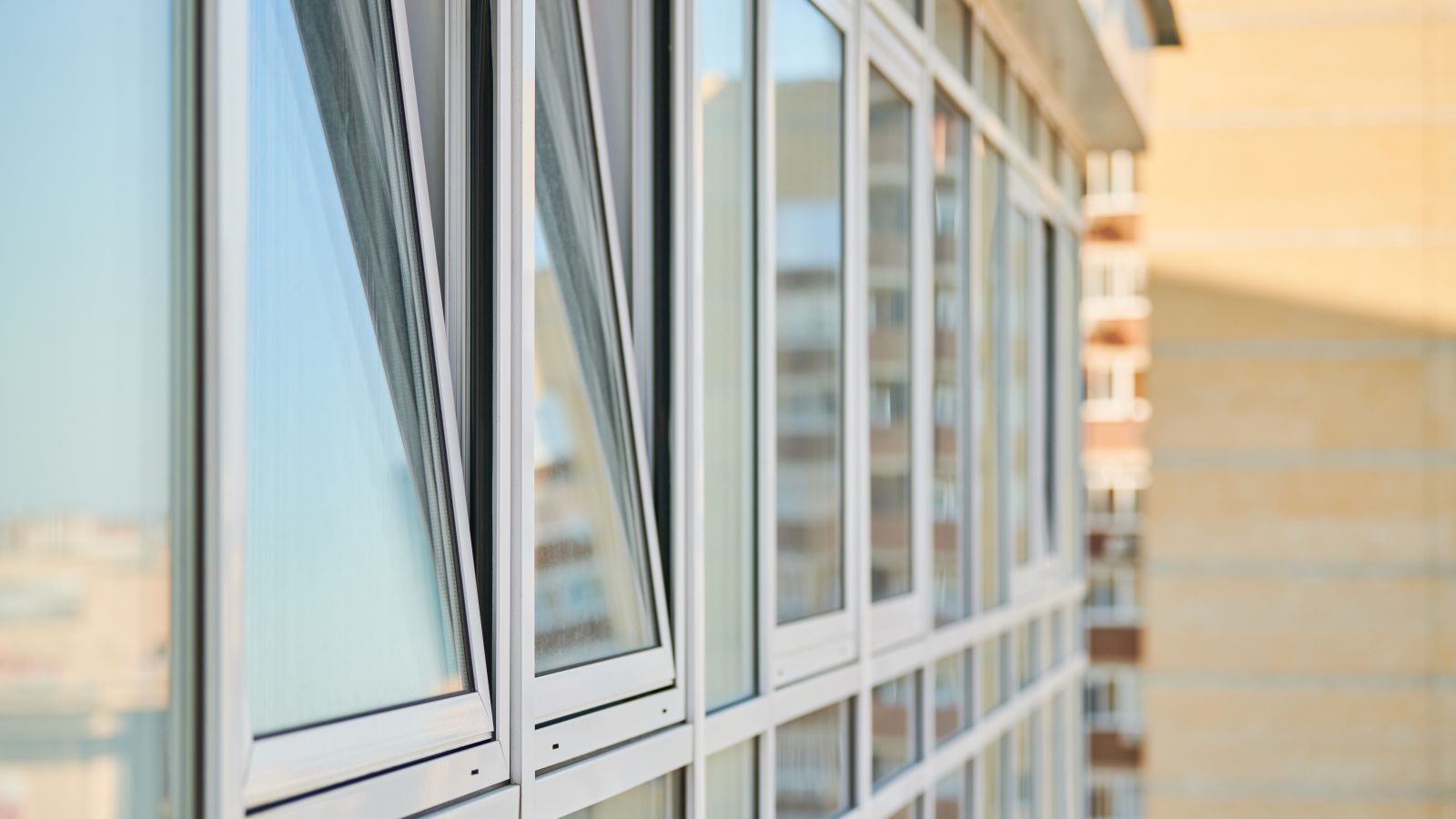
Optimierte Produktentwicklung
Die Produktion eines neuen Fensterrahmens erfordert die Herstellung eines neuen Extrusionswerkzeuges. Durch dieses Werkzeug wird die zähflüssige Kunststoffschmelze gedrückt, was dem Kunststoffstrang die finale Form verleiht. Über eine Kühlstrecke kühlt das Profil aus und kann in gewünschter Länge abgeschnitten werden. Bis das Profil den Qualitätsansprüchen entspricht werden bis zu zwölf Optimierungsschleifen durchgeführt. Jede Iteration benötigt eine Anpassung des Extrusionswerkzeuges.
Digitaler Zwilling simuliert Extrusionskopf
Um diesen Prozess zu beschleunigen, wurde in Kooperation mit dem jungen mittelständischen Unternehmen Ianus Simulation GmbH aus Dortmund ein digitaler Zwilling entworfen, mit dem die Strömungsvorgänge am Extrusionskopf simuliert werden können.
Der Bereich, in dem die Kunststoffschmelze fließt, wird dabei in hunderte kleine Kuben mit einer Kantenlänge von rund einem zehntel Millimeter zerlegt. Somit ist es möglich, zu jedem Zeitpunkt feinste Unterschiede in den Parametern Temperatur, Druck und Fließgeschwindigkeit der Schmelze zu berechnen. Die unterschiedlichen physikalischen Eigenschaften werden am Computer farblich dargestellt. Mit Hilfe der Simulation können die Ingenieure am Rechner erkennen, welche Konstruktion am besten geeignet ist, um den Qualitätsanforderungen des Kunden zu entsprechen.
Materialeinsatz halbiert
Für die herkömmlichen Testverfahren bis zum fertigen Profil wurden bisher circa zehn Tonnen PVC verbraucht. In der Regel benötigte das Engineering zwölf Proben. Dank der digitalen Lösung mittels des digitalen Zwillings - anstelle der vielfachen Produktion eines physischen Werkzeugs - konnte das Engineering die Probenzahl insgesamt halbieren und damit den Materialaufwand auf fünf Tonnen reduzieren. Somit wird nicht nur Material eingespart, sondern ebenfalls der Stromverbrauch um 1000kWh reduziert. Dies entspricht 408 kg CO2-Äquivalenten.
Die VEKA AG
... ist Spezialist für Fensterprofile aus Kunststoff und setzt auf digitale Produktentwicklungs-Tools, um die Qualität ihrer Fenster-Prototypen bereits in der frühen Entwicklungsphase deutlich zu steigern. So lässt sich die Anzahl von erforderlichen Iterationsschleifen bis zur Marktreife halbieren, mit dem Vorteil einer drastischen Material- und Energiereduzierung.
Technologie
Fähigkeit der KI: Simulation
KI-Modell: Digitaler Zwilling bzw. Simulation
Wertschöpfung
Phase: Entwicklung
Ziel der KI: Optimierung der Strömungsvorgänge im Extrusionskopf
Ressourceneffizienz
Pro entwickeltem Fensterrahmenprofil:
Materialeinsparung von 5t Primär- und Sekundärmaterial (PVC)
Reduktion des Stromverbrauchs um 1000 kWh