KI-basierte Qualitätsbestimmung für Tiefdruckzylinder
Die 4Packaging GmbH ist Hersteller von sogenannten Tiefdruckzylindern. Die Fertigung dieser Zylinder ist ein wichtiger Prozess zur Herstellung von Verpackungen. Die Qualität der Zylinder bestimmt dabei die Optik der finalen Verpackungen. Künstliche Intelligenz soll bei der Einsparung von Materialien und Energie im Produktionsprozess, bei der Bestimmung der Qualitätsgüte sowie bei der visuellen Qualitätskontrolle helfen. Hierfür werden zusätzliche Sensoren, sogenanntes Retrofitting, an den Maschinen- und Anlagen von 4Packaging angebracht. Zusätzlich werden bestehende Sensorströme und weitere Bilddaten analysiert und je Anwendungsfall zusammengeführt.
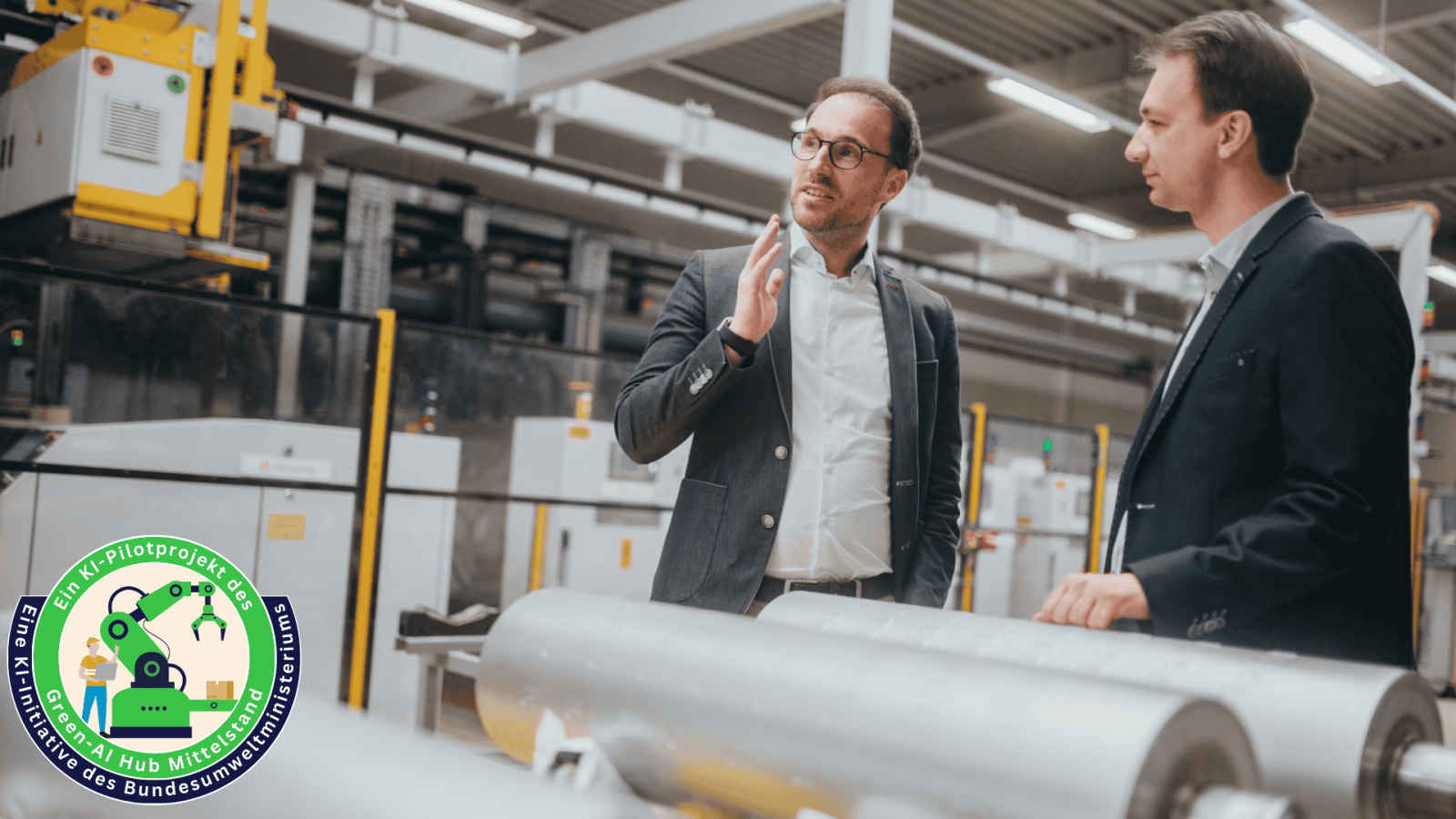
Innovative Produktion von Tiefdruckzylindern im Teutoburger Wald
Die 4Packaging GmbH ist ein Familienunternehmen, gegründet im Jahr 2000, mit Sitz in Dissen am Teutoburger Wald in Niedersachsen, in der Nähe von Osnabrück. Rund 120 Mitarbeitende kümmern sich um Prozesse, die vor dem eigentlichen Druck von Verpackungen stattfinden: Artwork und Reproduktion, Verpackungsentwicklung in 3D sowie die Präge- und Tiefdruckformherstellung. Dabei ist insbesondere die Tiefdruckformherstellung geprägt von Material- und Energieeinsatz und der Gewährleistung einer hohen Qualität.
4Packaging recycelt die verwendeten Tiefdruckzylinder im Rahmen der Tiefdruckformherstellung. Dies ist mit einem Blatt Papier und einem Bleistift vergleichbar, wobei das Blatt Papier stets wiederverwendet wird und eine neue Beschriftung durch einen Radierer ermöglicht wird. In der Praxis schaut dies anders aus: Hierfür werden Chrom und Kupfer im Mikrometerbereich auf den Zylinder ab- und aufgetragen. Die Kupferschicht dient der Gravur des Druckbildes. Die Chromschicht macht die Zylinder widerstandsfähiger, sodass die Druckform im Druckprozess länger eingesetzt werden kann. Das Auf- und Abtragen ist energieintensiv, so werden zum Beispiel chemische Lösungen im galvanischen Prozess benötigt, um die Kupferschicht aufzutragen. Viele kleine Parameter, wie die Einstellungen bei den Maschinen und die Beschaffenheit der Tiefdruckzylinder können die Qualität der Tiefdruckzylinder und damit das Druckergebnis beeinflussen.
Der technologische Wandel und neue Anforderungen der Kunden von 4Packaging erfordern kontinuierliche Anpassungen in den Prozessen, denen 4Packaging stets innovativ begegnet. 4Packaging hat weltweit als erster Graveur eine automatisierte Produktionslinie installiert und seither kontinuierlich erweitert und modernisiert. Die digitale Entwicklung von Verpackungen in 3D ermöglicht es den Kunden, ihre Vorstellungen digital umzusetzen, ohne Ressourcen für eine physische Entwicklung aufwenden zu müssen.
Herausforderung: Verbesserung der Prozessqualität in der Galvanik
Die Gewährleistung einer zuverlässigen Prozessqualität ist bei der Herstellung von Tiefdruckzylindern von hoher Bedeutung. Kleinste Fehler, bspw. bei der sogenannten Entfettung, können zu qualitativ schlechten Tiefdruckzylindern führen, die nachgelagert im Druckprozess unbrauchbar sind.
Weiterhin wird die Qualität des Tiefdruckzylinders durch die Galvanotechnik bestimmt. Die Galvanik bezeichnet ein elektrochemisches Verfahren zum Aufbringen von feinen Metallschichten auf einer metallischen oder sonstigen leitenden Oberfläche, z. B. Kupfer und Chrom. Dabei bestimmen verschiedenen Parameter die Qualität der Beschichtung, bspw. der pH-Wert, die Stromdichte, die Badtemperatur, die Dauer oder auch der Verschmutzungsgrad des Bades. Aktuell werden die Bäder manuell überwacht, indem Proben der chemischen Bäder zur Analyse ins Labor geschickt werden.
Der Green-AI Hub Mittelstand setzt im Pilotprojekt zusätzliche Sensoren ein, um die chemischen Bäder kontinuierlicher zu überwachen und Störquellen frühzeitig zu erkennen. Dadurch wird die Prozessqualität in der Galvanik deutlich verbessert.
Automatisierung und Optimierung der Qualitätsbestimmung durch Künstliche Intelligenz
Künstliche Intelligenz hilft 4Packaging die Einflüsse der verschiedenen Prozessparameter auf die Qualität besser zu verstehen sowie die Qualität ihrer Produkte kontinuierlich auf Basis der visuellen Bild- und Maschinendaten zu bestimmen.
Zum Einsatz kommen dabei Künstlich Neuronale Netze (KNN) zur Analyse der Sensordaten, die aus den bisherigen Sensoren der Maschinen- und Anlagen stammen, jedoch durch zusätzlich angebrachte Sensorik bei den chemischen Bädern, sogenanntes Retrofitting, im Rahmen des Green-AI Hub Pilotprojektes ergänzt wurden. Das neuronale Netz wird zur Bestimmung der Qualität des Tiefdruckzylinders verwendet. Ergänzt wird die KI, um den Einsatz von Computer Vision (Bildverarbeitung), die automatisiert Bildaufnahmen von den Tiefdruckzylindern nach Fehlern untersucht und den Fehlertyp einordnet.
Für den Einsatz beider Technologien, d.h. neuronale Netze sowie Computer Vision, sind große Datenmengen notwendig sowie sogenannte Labels, sprich die Kategorien, die einem Datensatz zugeordnet werden. Beispielsweise werden beim Computer-Vision-Modell nicht nur die Bilddaten benötigt, sondern auch eine Markierung, wo sich welche Fehler befinden. Die Aufbereitung des Datensatzes für das Computer-Vision-Modell ist anfänglich ein manueller Prozess, d.h. die Markierungen werden von einer Person vorgenommen. Nach dem Training eines ersten Computer-Vision-Modells, kann dieser Datenaufbereitungsschritt durch das bestehende Modell automatisiert werden, sodass lediglich eine Bestätigung und eine eventuelle Korrektur bei falsch interpretierten Fehlererkennungen erfolgt.
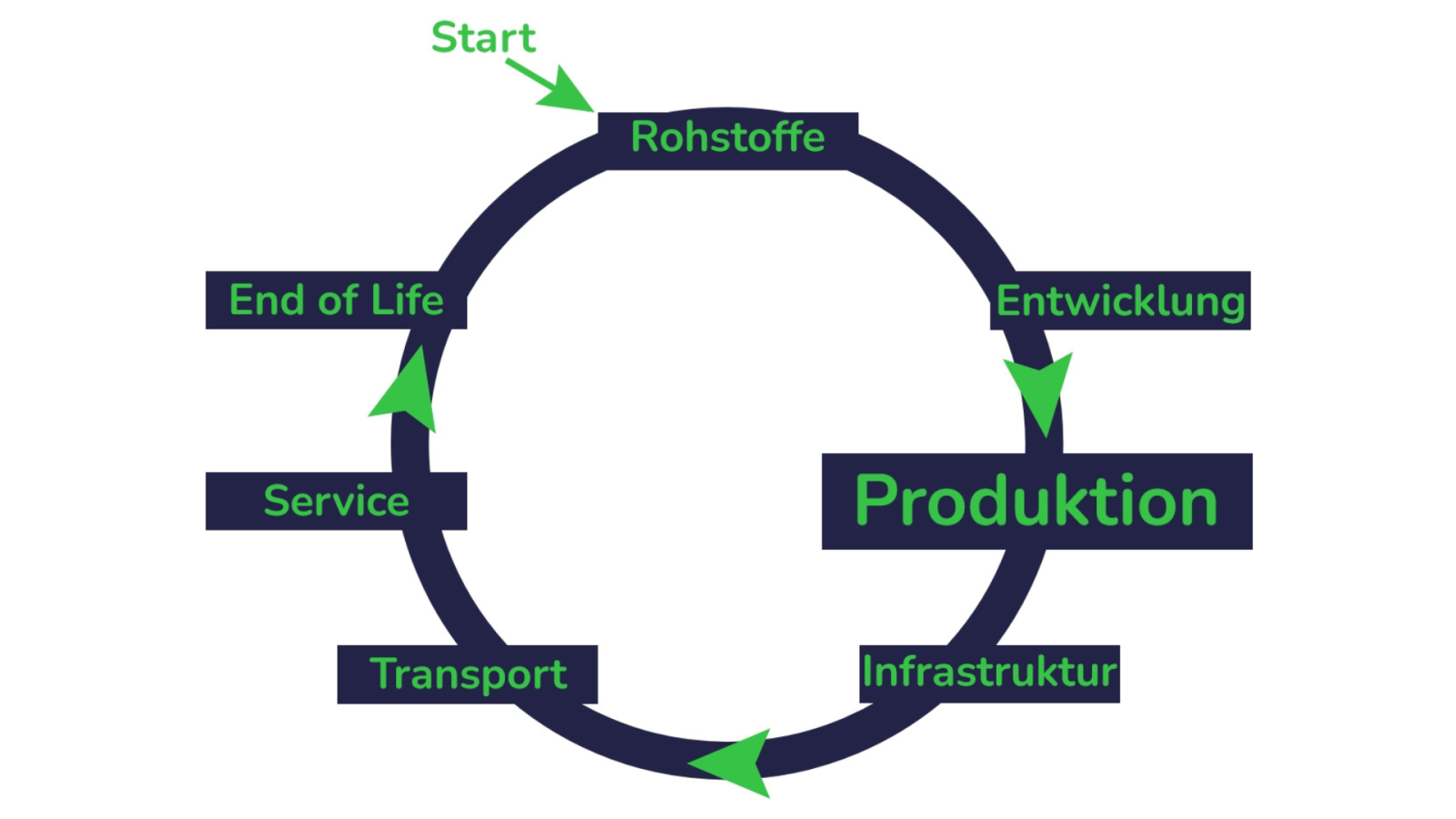
Ressourceneinsparung durch KI-basierte Qualitätsbestimmung
Die KI-basierte Qualitätsbestimmung bei 4Packaging wird händische Prüfungen zur Qualität automatisieren, sodass Abweichungen im Prozess frühzeitiger erkannt werden. Durch die Prozessverbesserungen mithilfe der KI-basierten Qualitätsbestimmung verspricht sich 4Packaging die mittelfristige Reduktion fehlerhafter Tiefdruckzylinder im Produktionsprozess um 20 Prozent, auf das Jahr gerechnet wären dies bis zu 403 Zylinder.
Dabei können Einsparpotentiale sowohl beim Carbon Footprint als auch beim Material Footprint, der den lebenszyklusweiten Materialaufwand quantifiziert, erreicht werden. Mit dem Einsatz von Künstlichen Neuronalen Netzen (KNN) zur Analyse der Sensordaten und dem Einsatz von Computer Vision könnten bezogen auf die Jahresproduktion der Carbon Footprint zwischen 9-12t CO₂-Äquivalente und der Material Footprint um 26-73t CO₂-Äquivalente verringert werden.
Weitere Berichterstattung zum KI-Pilotprojekt
Das Handelsblatt hat das KI-Pilotprojekt 4Packaging besucht sowie Bundesumweltministerin Steffi Lemke hierzu interviewt, den vollständigen Artikel finden Sie hier.
Vorstellung des Green-AI Hub-Pilotprojekts „KI-basierte Qualitätsbestimmung für Tiefdruckzylinder“ - 10:37 min.
- Henning Hacker, 4Packaging GmbH
- Lukas Schießer, Deutsches Forschungszentrum für Künstliche Intelligenz GmbH
Technologie
Fähigkeit der KI: Datenanalyse und Bilderkennung
KI-Modell: Künstlich Neuronale Netze (KNN) und Computer Vision
Wertschöpfung
Phase: Produktion & Qualitätskontrolle
Ziel der KI: Automatisierung manueller Prozesse zur Qualitätsprüfung
Ressourceneffizienz
Einsparungen Carbon Footprint: 9-12t CO₂-Äquivalente
Einsparungen Material Footprint: 26-73t CO₂-Äquivalente
Mittelfristige Reduzierung der Fehlerquote im Produktionsprozess um 20 Prozent