Resource-saving tool monitoring through federated learning
Milling tools rarely last exactly as long as planned - sometimes they break prematurely, and they are often replaced prematurely. At the Bosch site in Homburg, edge computing is used to monitor the milling process. The aim is to determine the wear on the tools using a federated learning network and thus determine the optimum time for replacement. This reduces tool breakages and rejects, and ensureseach tool is utilised in a more material and energy-efficient manner.
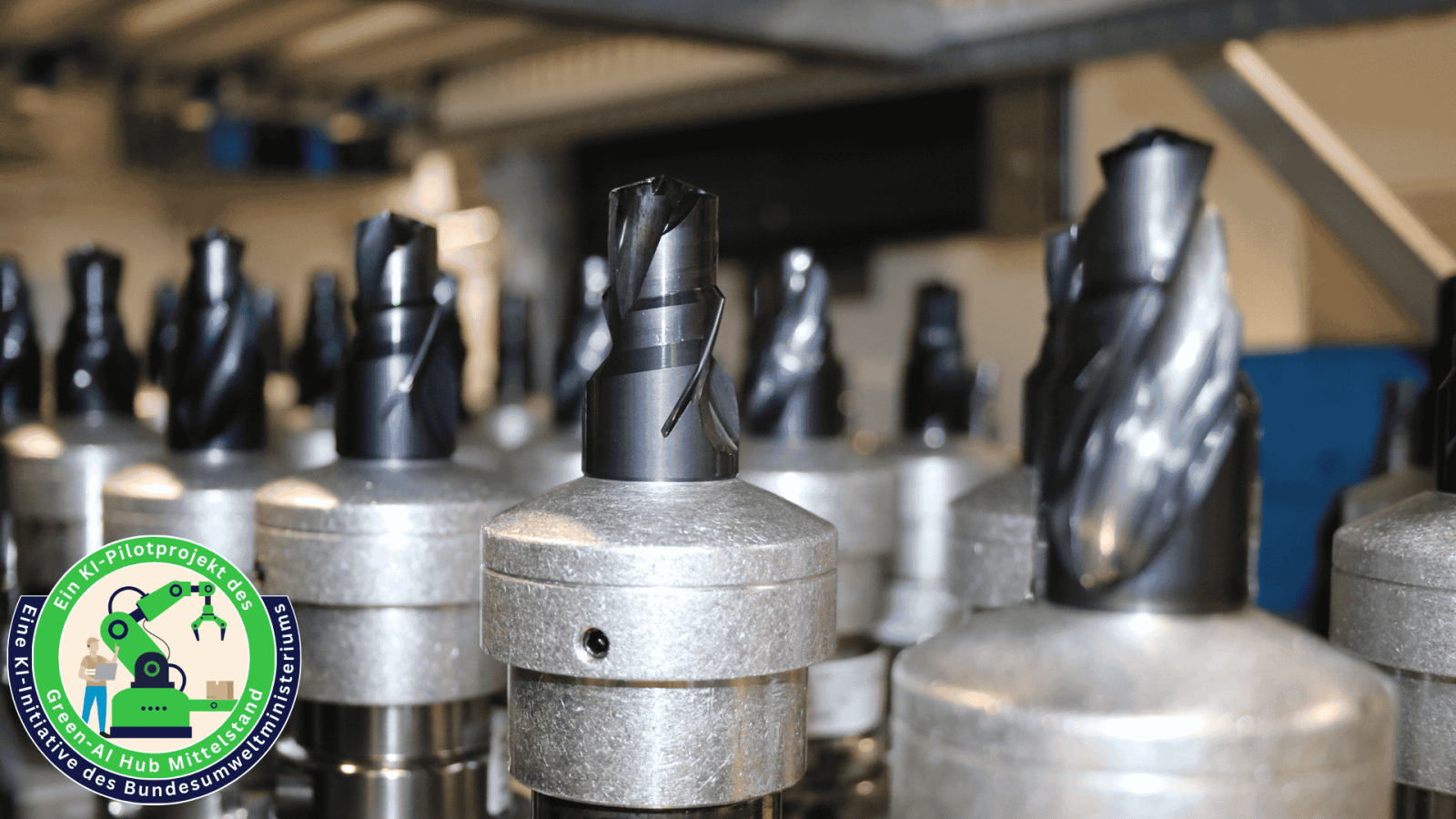
Decades of experience in injector and engine component manufacturing
The Homburg production plant of the Robert Bosch GmbH has been manufacturing injectors and components for diesel and hydrogen systems for decades. Up to now , large batch sizes in machining have required static tool change intervals based on conservative tool life. This leads to additional downtime and reduces resource efficiency because tools are reground or replaced prematurely.
Challenge: The quantity and type of tools within the company varies greatly
- Wide variation in tool life
- Premature replacement causes additional consumption of carbide and energy in the grinding process
- Despite a safety reserve, tool breakages occur that render workpieces unusable
- Very different tools require AI systems for each tool or modern aggregation methods
Solution through federated learning
The milling machine is retrofitted with additional sensors: current clamps measure the spindle current, a sound sensor listens to the milling process, and vibration sensors and the axis currents provide further signals. An edge computer collates and stores this data. Furthermore, all cutter changes and the associated reasons are documented. This data set is used to train individual models to determine the tool status and detect anomalies. Models of different tools are to be merged using federated learning to create a global model that works across tools and machines.
AI-supported tool monitoring with the help of sensor technology
AI-supported tool monitoring has a direct impact on the machining value chain : fewer premature changes and no breakages mean more stable cycles, less rework and lower stocks of replacement tools. This increases the availability and overall equipment effectiveness of the line, while reducing material and energy consumption. The solution can be rolled out 1:1 to other milling, turning and drilling centres, as only sensors need to be added and the model imported. In this way, Bosch in Homburg is creating a scalable blueprint use case that improves productivity, costs and sustainability at the same time.
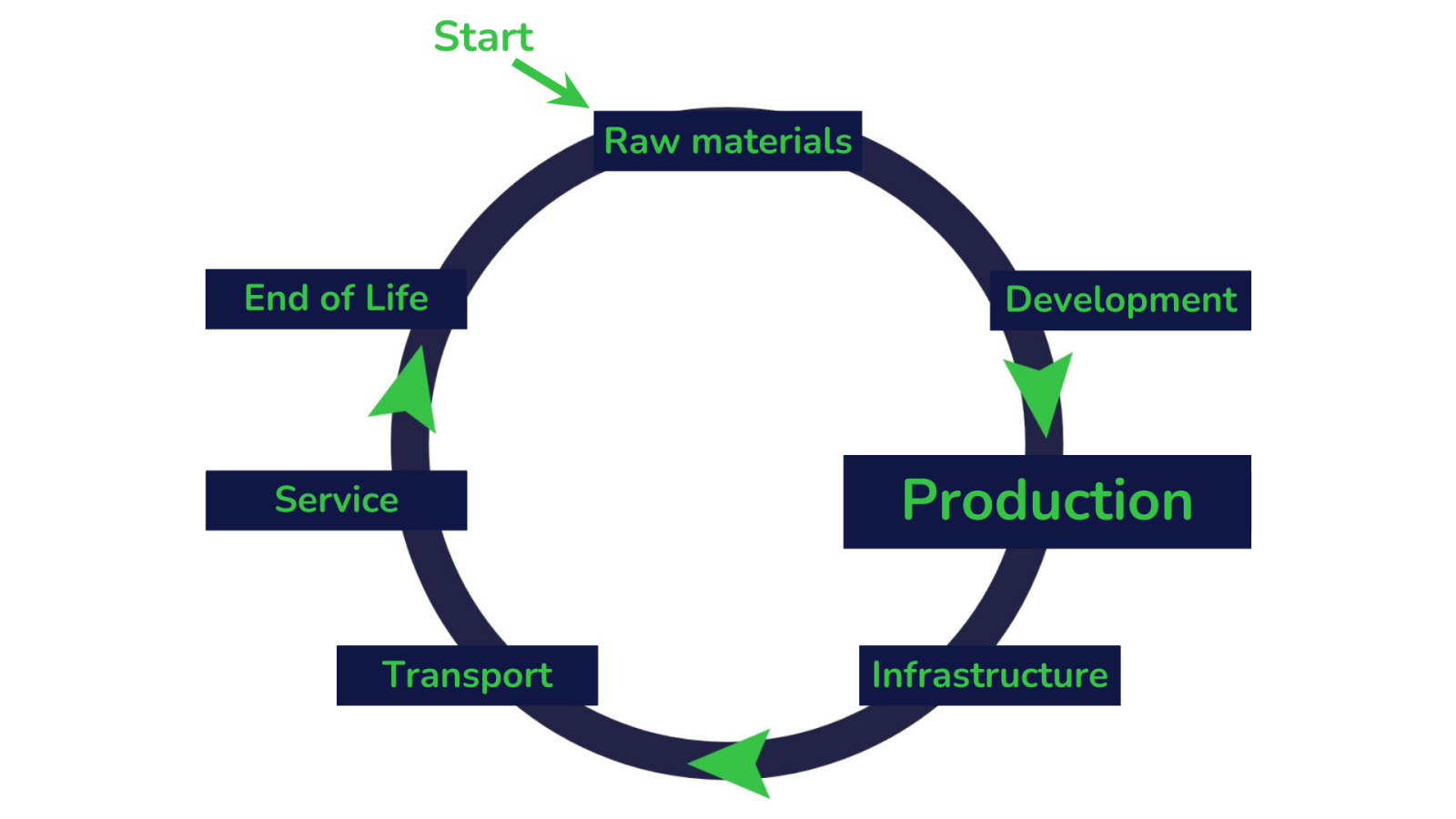
Reduced material usage with unchanged cycle time
Every prematurely discarded milling cutter not only means hazardous waste from high-alloy tool steel, but also a scrapped workpiece, additional set-up time and additional transport for regrinding. AI-supported wear detection extends the service life of the tools by around 10 percent. For each milling machine, around 52 kg of titanium-aluminium-nitride-coated special steel remains in the tool each year, and 150 kg of component steel remains in the value stream instead of in the scrap container. Fewer replacement orders reduce logistics routes and energy for the grinding and cleaning process; the Edge system can be retrofitted without machine conversion. At the same time, the early warning of breakages prevents rejects, cooling lubricant and chemical consumption. The bottom line is that material usage, processing energy and CO₂ are reduced - while the cycle time remains unchanged.
Robert Bosch GmbH is one of the world's largest technology and service companies. In the Mobility, Industrial Technology, Consumer Goods and Energy & Building Technology divisions, Bosch develops and manufactures solutions for industry, everyday life and mobility. The Homburg plant in Saarland has been producing high-precision injection systems for diesel and, increasingly, hydrogen applications for more than 60 years and is continuously working on energy-efficient manufacturing in the production network. Bosch employs 429,400 associates worldwide.
Technology
AI capability: Prediction of mould condition and anomaly detection
AI models: Resource-saving tool monitoring through federated learning
Value creation
Phase: Production
Aim of AI: Optimisation of tool utilisation, detection of anomalies
Resource efficiency
The AI-controlled, needs-based tool change saves around 52 kg of high-alloy tool steel and around 150 kg of component steel per milling machine per year.