Predictive maintenance using acoustic signals
Injection moulding is a manufacturing method in which the material is first liquefied and then injected under pressure into a desired shape. One disadvantage of the process is the time- and resource-intensive maintenance of the machines. INDIA-DREUSICKE Berlin, a specialist in the field of plastics and steel processing, was able to decisively improve maintenance times by using an AI system that analyses the condition of the equipment by means of audio recognition. This reduced the use of resources, improved plannability and avoided production downtimes.
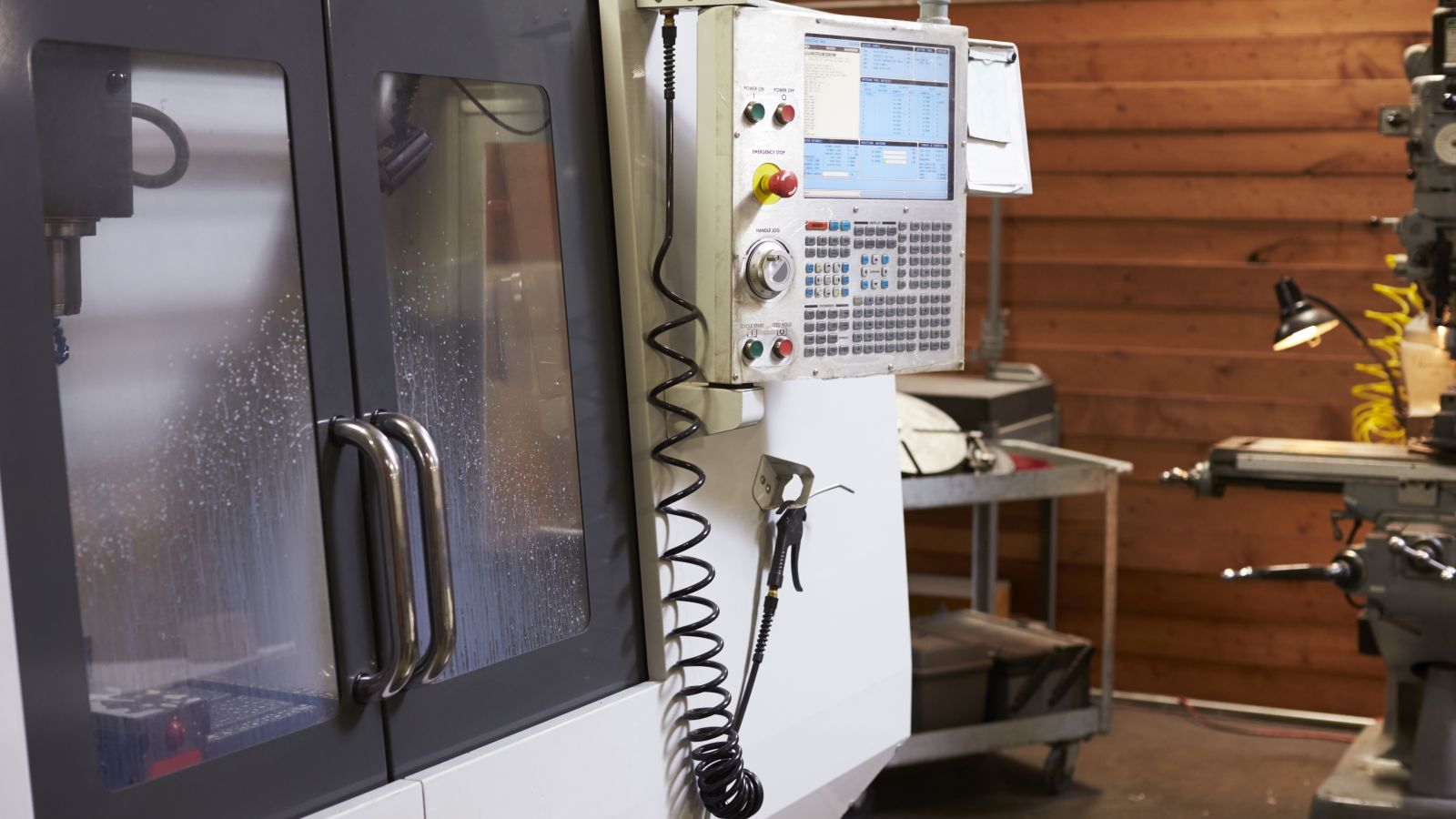
Company presentation incl. initial situation
INDIA-DREUSICKE Berlin is spezialised in the field of plastics processing and the machining of steel. Founded in 1929, the company manufactures, among other things, handlebar accessory parts for the automotive industry, components and housings for telecommunications boxes as well as components for street lamps. For the production of the moulded parts, the company relies on the injection moulding process, among other things.
The challenge
The injection moulding machines must be regularly maintained, the injection moulds disassembled and precision parts lubricated. Maintenance is a particularly time- and resource-intensive process and is carried out every 3-5 days. This value is based on the experience of employees. Due to different plant designs, the maintenance times cannot be determined exactly. If maintenance is carried out too late, for example, the moulds and the products are damaged, leading to the production of rejects. In the worst case, production comes to a standstill.
Solution through the use of artificial intelligence
In order to determine the ideal time for maintenance and to detect malfunctions at an early stage, an AI system is used which analyses the condition of the system by means of audio recognition and automatically shuts it down when maintenance is required. In the first step, data was collected from the plants over a period of more than twelve months using corresponding software and various microphones. This data was then used to train the AI system.
Value creation
Improving maintenance leads to fewer repairs and thus saves on spare parts and resources. In addition, improved plannability can reduce costs and working hours and avoid plant shutdowns.
Plattform Lernende Systeme – Die Plattform für Künstliche Intelligenz (2021): KI im Mittelstand – Potenziale erkennen, Voraussetzungen schaffen, Transformation meistern, Bericht, Plattform Lernende Systeme – Die Plattform für Künstliche Intelligenz, München.
INDIA-DREUSICKE Berlin
…is a specialist in the field of plastics processing and the machining of steel and relies on injection moulding for many of the components it produces. To determine the ideal time to maintain the machines, the company relies on AI-based audio recognition, an application of predictive maintenance. This saves spare parts and the improved planning capability reduces costs and downtime.
Technology
AI capability: understand, communicate
AI model: computer audition, prediction
Value creation
Phase: production
Aim of AI: sound recognition
Resource efficiency
Longer service life of components
Less downtime
Savings in costs and labour time